Preliminary Field Studies on Worker Exposures to Volatile Chemicals during Oil and Gas Extraction Flowback and Production Testing Operations
Posted on by
This blog describes NIOSH evaluations of worker exposures to specific chemicals during oil and gas extraction flowback and production testing activities. These activities occur after well stimulation and are necessary to bring the well into production. Included are descriptions of initial exposure assessments, findings, and recommendations to reduce worker exposures to potential hazards. Further details about these assessments can be read in a recently published peer-reviewed journal article, “Evaluation of Some Potential Chemical Exposure Risks during Flowback Operations in Unconventional Oil and Gas Extraction: Preliminary Results”.[i]
Flowback Operations
Flowback refers to process fluids that return from the well bore and are collected on the surface after hydraulic fracturing. In addition to the mixture originally injected, returning process fluids can contain a number of naturally occurring materials originating from within the earth, including hydrocarbons such as benzene. After separation, flowback fluids are typically stored temporarily in tanks or surface impoundments (lined pits, ponds) and recovered oil is pumped to production tanks, which are fixed systems at the well pad. Figure 1 shows two separators (white), six flowback tanks (tan), and multiple water tanks (yellow) arranged in a typical side-by-side manner in the background of the photo. Workers periodically gauge the fluid levels in both flowback and production tanks with hand-held gauges (sticks and tapes) through access hatches at the top of the tank. (Figure 2)
Initial Exposure Assessments during Flowback and Production Testing Operations
NIOSH exposure assessments included short-term and full-shift personal breathing zone and area air sampling for exposures to benzene and other hydrocarbons using standard methods and analyses listed in the NIOSH Manual of Analytical Methods.[ii] Real-time, direct reading instruments were also used to characterize peak and short-term exposures to workers and various workplace areas for volatile organic compounds, benzene, carbon monoxide, hydrogen sulfide, and flammable/explosive atmospheres. We conducted biological monitoring by collecting pre- and post-shift urine samples from flowback workers to evaluate exposure to benzene. Benzene metabolites found in a worker’s urine indicate some level of exposure during the work shift. Benzene is an exposure concern because the Department of Health and Human Services’ National Toxicology Program has determined that it is a known carcinogen (i.e., can cause cancer).[iii] The International Agency for Cancer Research and the EPA have also determined that benzene is carcinogenic to humans.[iv,v]
Findings
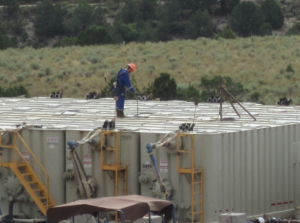
Workers gauging tanks can be exposed to higher than recommended levels of benzene. The average full-shift time-weighted average (TWA) personal breathing zone benzene exposure (± 1 standard deviation) for workers gauging flowback or production tanks (n=17) was 0.25 ± 0.16 parts per million (ppm). Fifteen of these 17 samples exceeded the NIOSH recommended exposure limit (REL) of 0.1 ppm (0.32 mg/m3)[vi]. (This REL is a quantitative value based primarily on analytical limits of detection. NIOSH recommends that occupational exposures to carcinogens be limited to the lowest feasible concentration). Because the flowback technicians’ work shifts were 12 hours, a reduction factor of 0.5 was calculated to modify the American Conference of Governmental Industrial Hygienists (ACGIH) threshold limit value for benzene from 0.5 ppm to 0.25 ppm. Two of 17 samples met or exceeded the ACGIH unadjusted value of 0.5 ppm value; six of 17 exceeded the adjusted value of 0.25 ppm.[vii] Task-based personal breathing zone samples for benzene collected during tank gauging on flowback tanks exceeded the NIOSH short-term exposure limit (STEL) for benzene (1 ppm as a 15-minute TWA).[ii] At several sites, direct-reading instrumentation measurements detected peak benzene concentrations at open hatches exceeding 200 ppm.
The average full-shift personal breathing zone benzene exposures (± 1 standard deviation) for workers not gauging tanks (n=18) was 0.04 ± 0.03 ppm. The difference in mean personal breathing zone benzene exposures between those who gauged tanks and those who did not was statistically significant. Seventeen of the 18 samples were below the REL as a full-shift TWA for those not gauging tanks. None of the 35 full-shift personal breathing zone sampling results exceeded the Occupational Safety and Health Administration (OSHA) permissible exposure limit for benzene of 1 ppm for general industry (29 CFR 1910.1028) or 10 ppm for the oil and gas drilling, production, and servicing operations sector exempt from the benzene standard (29 CFR 1910.1000 Table Z-2).[viii] Exposures to other measured hydrocarbons (e.g., toluene, ethyl benzene, and xylenes) did not exceed any established occupational exposure limits.
For the biological monitoring, we used s-phenyl mercapturic acid, a specific metabolite of benzene that can be measured in urine. We compared the results to the ACGIH Biological Exposure Index (BEI) for occupational benzene exposure.[iii] The benzene BEI represents the concentration of metabolites most likely to be observed in specimens collected from healthy workers exposed to the ACGIH TLV of 0.5 ppm. None of the biological monitoring samples were found to exceed the ACGIH BEI.
Direct reading instruments identified instances of short-term flammable atmosphere measurements as high as 40% of the lower explosive limit (LEL) adjacent to separators and flowback tanks; in general, a concentration of 10–20% of the LEL is considered a risk for fires and is the typical alarm settings for direct reading personal and fixed flammable gas monitors.
Preliminary Conclusions
These findings suggest that benzene exposure can exceed the NIOSH REL and STEL and present an occupational exposure risk during certain flowback work activities. Based on these preliminary studies, primary point sources of worker exposures to hydrocarbon vapor emissions are opening thief hatches and gauging tanks; additional exposures may occur due to fugitive emissions from equipment in other areas in the flowback process (e.g., chokes, separators, piping, and valves), particularly while performing maintenance on these items. The NIOSH research found that airborne concentrations of hydrocarbons, in general, and benzene, specifically, varied considerably during flowback and can be unpredictable, indicating that a conservative approach to protecting workers from exposure is warranted. Hydrocarbon emissions during flowback operations also showed the potential to generate flammable and explosive concentrations depending on time and where measurements were made, and the volume of hydrocarbon emissions produced.
Recommendations for Protecting Workers
Based on workplace observations at the sites visited, NIOSH researchers identified a number of general recommendations to reduce the potential for occupational exposure:
- Develop alternative tank gauging procedures so workers do not have to routinely open hatches on the tops of the tanks and manually gauge the level of liquid.
- Develop dedicated sampling ports, other than the thief hatches, that minimize workers’ exposures to volatile organic compound emissions while manually tank gauging.
- Provide worker training to ensure flowback technicians understand the hazards of exposure to benzene and other hydrocarbons and the importance of monitoring atmospheric conditions for LEL concentrations.
- Limit the time spent in proximity to hydrocarbon sources.
- Monitor workers to determine their exposure to benzene and other contaminants.
- Establish a controlled perimeter (similar to the high pressure zone established during hydraulic fracturing) around flowback tanks. Limit entry and require that any portable tents or sunshades remain outside and upwind of the controlled area.
- Provide workers with calibrated portable flammable gas monitors with alarms at appropriate levels. The actions to be taken if the alarm sounds should be defined before the detector system is put into use.
- Use appropriate respiratory protection in areas where potentially high concentrations of hydrocarbons can occur as an interim measure until engineering controls are implemented. Note that OSHA regulations (29 CFR 1910.134) require a comprehensive respiratory protection program be established when respirators are used in the workplace.4
- Use appropriate impermeable gloves to protect against dermal exposures during work around flowback and production tanks and when transferring process fluids.
Help Wanted
NIOSH is looking for additional partners in drilling and well servicing to work with us to further evaluate worker exposures to these chemicals and other hazards and to develop controls, as needed. To investigate whether workers are exposed to toxic chemicals at hazardous concentrations in this rapidly expanding industry and to address the existing lack of information on occupational chemical exposures, NIOSH initiated the NIOSH Field Effort to Assess Chemical Exposures in Oil and Gas Extraction Workers. NIOSH conducted a comprehensive exposure assessment to characterize worker exposure to crystalline silica in this process. The results from this evaluation and recommendations for controlling worker exposure to crystalline silica during hydraulic fracturing have been disseminated in trade association journals, a previous NIOSH science blog, an OSHA-NIOSH Hazard Alert, and a peer-reviewed publication. Furthermore, in a recent NIOSH science blog posting, we addressed reports made known to NIOSH of recent fatalities of workers who were gauging flowback or production tanks or involved in transferring flowback fluids at the well site. Other potential occupational exposures can include hydrocarbons, lead, naturally occurring radioactive material (NORM), and diesel particulate matter, which have not been fully characterized. If you have questions or wish to participate in any aspects of this effort, please contact us via the blog comment box below.
Eric J. Esswein, MSPH, CIH, John Snawder, PhD, DABT, Bradley King, MPH, CIH, Michael Breitenstein, BS, and Marissa Alexander-Scott, DVM, MS, MPH.
Eric Esswein and Bradley King are with the NIOSH Western States Office in Denver, CO. John Snawder, Michael Breitenstein, and Marissa Alexander-Scott are with the NIOSH Division of Applied Research and Technology (DART) in Cincinnati, OH. The authors would like to acknowledge Belinda Johnson (NIOSH DART) for her efforts and contributions prior to and during the field studies.
Notes:
NIOSH notified company representatives of these findings and provided reports with recommendations to control exposure to benzene and other volatile materials that may be present. We provided all monitored workers with a confidential letter explaining the results of the evaluation and contact information for questions.
The objective of this blog entry is to describe the NIOSH Field Effort to characterize worker exposures in the oil and gas extraction industry, specifically during post-drilling flowback operations. To keep the blog discussion focused on worker health, we may choose not to respond to or to post comments that do not pertain to worker exposures.
References
[i] Esswein E, Snawder J, King B, Breitenstein M, Alexander-Scott M, Kiefer M [2014]. Evaluation of Some Potential Chemical Exposure Risks during Flowback Operations in Unconventional Oil and Gas Extraction: Preliminary Results. Journal of Occupational and Environmental Hygiene 11(10):D174–D184.
[ii] NIOSH [2003]. NIOSH manual of analytical methods (NMAM®). 4th ed. Schlecht P.C., O’Connor P.F., eds. Cincinnati, OH: U.S. Department of Health and Human Services, Centers for Disease Control and Prevention, National Institute for Occupational Safety and Health, DHHS (NIOSH) Publication 94–113 (August 1994); 1st Supplement Publication 96–135, 2nd Supplement Publication 98–119; 3rd Supplement 2003–154. [http://www.cdc.gov/niosh/docs/2003-154/].
[iii] NTP [2011]. Report on Carcinogens, Twelfth Edition. Research Triangle Park, NC: U.S. Department of Health and Human Services, Public Health Service, National Toxicology Program. 499 pp. [http://ntp.niehs.nih.gov/ntp/roc/twelfth/roc12.pdf].
[iv] IARC [2012]. Chemical agents and related occupations, volume 100F: A review of human carcinogens. Benzene. Lyon, France: International Agency for Research on Cancer, pp 249–294. [http://monographs.iarc.fr/ENG/Monographs/vol100F/mono100F-24.pdf].
[v] EPA [2009]. Integrated Risk Information System (IRIS) on Benzene. Washington, DC: U.S. Environmental Protection Agency, National Center for Environmental Assessment, Office of Research and Development. [http://www.epa.gov/iris/subst/0276.htm]
[vi] NIOSH [2010]. NIOSH pocket guide to chemical hazards. Cincinnati, OH: U.S. Department of Health and Human Services, Centers for Disease Control and Prevention, National Institute for Occupational Safety and Health, DHHS (NIOSH) Publication No. 2010-168c. [http://www.cdc.gov/niosh/npg/].
[vii] ACGIH [2014]. 2014 TLVs® and BEIs®: threshold limit values for chemical substances and physical agents and biological exposure indices. Cincinnati, OH: American Conference of Governmental Industrial Hygienists.
[viii] CFR. Code of Federal Regulations. Washington, DC: U.S. Government Printing Office, Office of the Federal Register.
23 comments on “Preliminary Field Studies on Worker Exposures to Volatile Chemicals during Oil and Gas Extraction Flowback and Production Testing Operations”
Comments listed below are posted by individuals not associated with CDC, unless otherwise stated. These comments do not represent the official views of CDC, and CDC does not guarantee that any information posted by individuals on this site is correct, and disclaims any liability for any loss or damage resulting from reliance on any such information. Read more about our comment policy ».
I’ve always thought that quoting the “average” (in this case, 0.04 ± 0.03 ppm for benzene) is an underestimation. Averages can easily fall below an OEL, and in this case, 0.04 falls well below 0.5ppm, and therefore is an underestimation. Any employer would look at this and immediately conclude that there is no exposure. I haven’t yet gone into the details of this data set or its statistical analysis, but I assume that it follows the commonly found lognormal distribution, in which case, including more reporting parameters would be useful to the reader, such as the UCL.
Thank you for your comment. This blog presents preliminary exposure assessments for workers conducting flowback and early production testing. The primary purpose of presenting data in the blog was to show there appear to be different exposure groups: workers gauging tanks: = 0.25 ± 0.16 parts per million (ppm) benzene, range = 0.01-0.59 ppm, and workers not gauging tanks: mean 0.04 ± 0.03 ppm benzene, range 0.004- 0.1 ppm.
As the title indicates, the data are preliminary and can be considered as range-finding in nature, and a small sample set. Also, the data are not generalizable nor to be used to predict exposures or make assessments for compliance purposes.
Although I am not a scientist, I do work in industry which requires PPE when exposure to chemicals are used. It would seem that OSHA and federal government and the Oil and Gas Industry would exercise on the extreme side of caution. Wokers should be required to wear PPE masks etc when coming in contact with flow back and production water , which obviously has benzene and many more hazardous chemicals. Many workers are effected by these exposures over extended periods per day over years. It is insane to think that these exposures even if miniscule at any given time are not harmful over long term exposures of years day in day out .
Also during flow back operations were this activity often happens in close proximity to residential communities and dense population areas presurized filtered control flow back containers should and must be used to prevent unintended exposure to persons nearby.
Your study indicates the benzene exposure from the flowback is the result of naturally occuring material from within the earth. Did you investigate the possibilty that the benzene exposures could occur because it was used as an ingredient or is a constituent of the orignally injected frack fluid in dry well conditions? Did you evaluate this aspect of potential benzene exposure?
Nice post and The information is very useful
Dear scientists,
I am really considering becoming a flowback operator and obviously 99% of the companies that do such operations don’t care for my health. But I want to do the job, it pays very well and I’d work 2 weeks on and 2 weeks off to travel.
I have noticed that all of these flowback guys out here don’t wear respirators or anything for breathing really. So here are my questions. I will definitely be manually gauging tanks, what kind of respirator will I need? And also, do benzene fumes absorb through the skin? If so, what kind of clothing can you suggest? I’d have to buy all this stuff as the company won’t pay for it. Thanks a lot for your time.
Thanks for contacting us. I’ve provided a response under each question.
“I will definitely be manually gauging tanks, what kind of respirator will I need?”
Proper respiratory protection is not really as simple as just recommending a respirator for a given job or potential chemical. The proper way to go about protection from air contaminants is for your employer to have a written respiratory protection program. This involves 1) Determination of the need for a respirator. Employers should evaluate work areas for inhalation (what you may breathe in) hazards. Is the exposure concentration of the contaminants, as determined by acceptable industrial hygiene methods, less than the NIOSH REL or other applicable exposure limit? If so, no respiratory protection is required. If contaminant concentrations do exceed safe limits, the employery should design engineering controls to eliminate the hazards, or less desirable, develop work practices that reduce or prevent worker exposures. Respirators should never be the primary solution to an exposure problem but, a last resort. 2) Proper selection of the respirator. NIOSH certifies and recommends respirators based on the chemical of concern and also the potential concentration encountered. This information may be found in the NIOSH Pocket Guide to Chemical Hazards (http://www.cdc.gov/niosh/npg/). 3) Medical clearance for the use of a respirator. A physician or qualified health professional will determine if you are healthy enough to wear a respirator. The use of a respirator is physically demanding and in some people claustrophobic. 4) Training in the proper use of a respirator. You will need to be trained on the specific respirator you will use. This training must include how to inspect your respirator, how to put it on (donning), check for leaks, and finally, how to take it off (doffing), clean and store it. You will need to be clean shaven whenever you wear the respirator. 5) Proper fit testing. A quantitative fit test of the respirator you will use is required.
The resources below will provide more information.
OSHA Respirator Quick Card: https://www.osha.gov/Publications/3280-10N-05-english-06-27-2007.html
OSHA Respiratory Protection Bulletin: https://www.osha.gov/dts/shib/respiratory_protection_bulletin_2011.html
NIOSH Guide to Respiratory Protection; http://www.cdc.gov/niosh/docs/87-116/
OSHA information on small business respiratory protection programs: https://www.osha.gov/Publications/3384small-entity-for-respiratory-protection-standard-rev.pdf
“Do benzene fumes absorb through the skin? If so, what kind of clothing can you suggest?”
Benzene will absorb through the skin but, typically that is the result of the liquid getting on you and not relatively low concentration of fumes in air. Typically, unless you splash yourself with liquid, long sleeve shirts and gloves will provide you with sufficient skin protection. Workers involved in Oil and Gas completion and production (where flowback and production monitoring occurs) activities are required by OSHA to wear flame retardant clothing. This is clothing that is made of materials or treated to be resistant to catching on fire. Because many of the jobs in oil and gas are done in the potential presence of flammable gas and vapors, your outermost layer of clothing must be flame retardant. If you purchase your own clothing, it must still meet the flame retardant standard.
“I’d have to buy all this stuff as the company won’t pay for it.”
Your employer is required to provide you with the clothing and protective equipment you will need. Because the potential for working in flammable atmospheres is present on these sites, any tools and equipment you use should be approved for use in hazardous/flammable atmospheres.
“I am really considering becoming a flowback operator and obviously 99% of the companies that do such operations don’t care for my health.”
In the interview process you should ask questions if you have concerns. A good company is going to train you how to do the job safely to protect you and your co-workers. There are a lot of resources available to help you.
Nice way to execute a post. I think you have done a fabulous work. Keep posting.
This is a very informative page. I really enjoyed reading the material you guys have posted up here.
I really like what NIOSH is doing here. Very positive influential stuff.
David
CEO/President
I attended the session this week by Todd at the OSHA Conference in Houston. Excellent work and great presentation. I was wondering about a few things.
1. Best Practices
It would seem there should be a literature search and or a reach out for best practices in procedures that can be shared and published. One would think there would be many sources to draw upon and review and some meaningful help would result. For example, upon initial opening of courses there is substantial flow until the tanks stored pressure relieves itself and equilibrium flow results between the rate of gas production and the flow capability of the events and open hatches. One wonders for example if this can be studied and correlated to crude types, tank geometry and vent details.
2. Pressure problem
It seems a lot of the tank gauging issue is really a tank pressure issue. If the tank pressure were reduced to basically nothing, (prior to opening), then opening the tank would make for no release. I believe there’s a need for measuring static pressure inside tanks prior to even your sampling and study. There may also be other factors important for correlating exposure to site conditions like: a) tank geometry vs. volume of contents, static pressure inside, barometric pressure, ambient temperatures, wind speed and direction, vent design and size (i.e. if flame arrestor what type?, manufacturer?, open pipe, screen – what size?), all of these issues define the likely pressure in the tank along with of course the nature of the VOC’s.
I would think it would be fairly easy to construct a pressure warning system, (simply a common magnahelic gauge on the side of the tank with a pet cock to indicate to a pumper that he is or is not likely to encounter severe flow when the lid is open). This would at least be a start.
I would think it also possible to construct a pressure balancing system, especially in a tank farm scenario. This could take many forms and would have to consider issues surrounding drawing air into tanks that could create more hazards. Nitrogen might also help here, but that also can create hazards.
3. Legislatively and code driven issues
Who is leading the charge to advocate for changes to federal laws and things like API standards that make for administrative things that do not help this situation at all? Is there someone leading this charge.
Anyway, just some thoughts. I am sure many have already been addressed but maybe there’s a nugget here somewhere that can help. Again, excellent work you guys are doing.
Thank you for your comment. NIOSH, OSHA and industry partners are conducting research to characterize, understand and ultimately control these safety and health hazards.
This is really a nice post, I understand this situation because here, in Spain we had problems with oil and gas workers. This post explains really well the problems with workers, I’ll share this on social networks to put pressure on the responsible people.
Daniel,
I really don’t know much about flowback but I do agree with protocols designed to enhance worker safety whenever possible. I’m glad these things are being done and that these chemicals can be stored in a safe manner for further uses. I am always concerned about contaminating our drinkable water storage areas as well as habitat for wildlife.
Excellent post this problem is very common and this is explained very well!
very good study of the benzene
This article is very interesting to me because I am looking start my career in this field… After reading this article I am so happy with my decision…
As an Oilfield Drilling Fluids Engineer/Guager/Pumper, expierience is the key, when
guagers line up tanks to recieve from dump valves on wells, compressors, & seperators
it depends on the flow rate after a Frac. it will be excessive, with lots of mixed gasses
at first until the well is flowed back, and regulated by the Rail Road Commission.
When a well is regulated on a choke, volumes of oil, gas, & water are calculated to
determine the correct flow rate after the Frac, and optimun flow rate for several months
production, then readjusted by Rail Road Commision.
Good article with excellent idea! I appreciate your post.Regards
Your latest updates are very informative from others. Thanks and Regards
How can I determine chemical exposure at a petroleum tank farm ? What are the exposure limits of VOCs fumes that are found at petroleum tank farm ?
Dear James,
Thanks for your inquiry. Determining risks for chemical exposures at petroleum tank farms is not trivial. Typically, trained industrial hygienists, or safety and health professionals conduct exposure assessment studies but this requires specialized knowledge and experience, calibration and use of sampling instrumentation, and may involve significant costs for analytical laboratory testing and interpretation of the results. Determining risks for chemical exposures may not be necessary at a tank farm if work involves manual tank gauging. This is because NIOSH (and OSHA) exposure assessment studies have already determined that significant exposure risks can be present but the risks depend on many factors including work practices, the type and configuration of the tanks, if the tanks are interconnected and if they are atmospherically vented. For example, NIOSH has determined that workers who manually gauge production and flowback tanks have greater for exposures to benzene (a chemical carcinogen) than workers who do not gauge tanks. Please see the NIOSH OSHA Hazard Alert on Tank gauging https://www.osha.gov/Publications/OSHA3843.pdf for detailed information on risks for exposures when working around tanks.
Additionally, our article in the Journal of Occupational and Environmental Hygiene lists the exposure criteria for several chemicals including benzene but describing all these criteria in this response involves far too much detail, so please read the article http://www.tandfonline.com/doi/pdf/10.1080/15459624.2014.933960 Please contact Eric Esswein (eje1@cdc.gov or 303 236-5946 at NIOSH for a more in-depth explanation of exposure assessments and more importantly, controls for exposures that can be used at petroleum tank farms to limit or prevent exposures.
I am trying to determine the potential health impacts of 3M Scotchkote Fusion Bonded Epoxy 6233 as it chalks off of stored pipes due to UV exposure. The MSDS for the material prior to coating the pipes shows carcinogenic and toxic properties, and I am concerned about inhalation risks at pipe storage locations, and ingestion risks from this material getting into drinking water supplies, and especially for persons using private springs and wells in karst areas where pipes are being installed. I am also concerned about pipeline worker safety.
I am not familiar with blogging. Can you e-mail me directly, or e-mail me that you have answered this question?
Thank you for your assistance.