Preventing Struck-by Fatalities Related to Excavator Quick Couplers, Buckets, and Attachments
Posted on by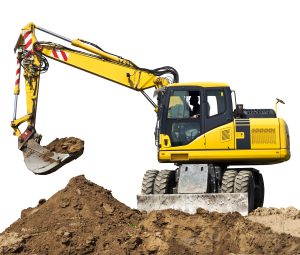
The 3rd annual National Stand-Down to Prevent Struck-by Incidents will take place April 11–15, 2022. As part of these efforts, NIOSH and others are highlighting the lethal struck-by risk related to excavator quick couplers. A quick coupler failure can cause the attachment to fall suddenly, causing death, injury, and/or damage to the excavator and attachment.
Background
Hydraulic excavators (Figure 1 and 2) are used in construction to move large quantities of earth. Many excavators have tracks for movement and are commonly called “trackhoes” or “backhoes.” An excavator quick coupling device (quick coupler) can save a lot of time on the job site, but when an excavator bucket unintentionally detaches from a quick coupler, worker fatalities can – and have – occurred. Quick couplers allow for the rapid change of buckets and other attachments on the end of excavator dipper arms. Depending on the design, they may be used to connect attachments remotely from the cab or may require the operator to complete the connection of the device manually on the ground by inserting a locking pin. Safety mechanisms are built into most modern quick couplers, but they are not fail-proof.
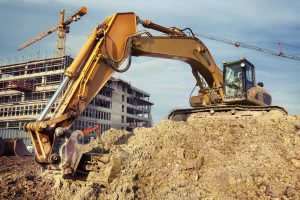
Struck-by incidents are a leading cause of death among construction workers [1], and since 1992 the leading cause of nonfatal injuries in the construction industry [2]. Excavators are dangerous to work around. The boom and dipper arm move quickly in small spaces such as a trench and carry extremely heavy loads. An excavator bucket can weigh 900 pounds while empty, and significantly more when holding soil or rock, making a failure very dangerous.
Three deaths have been reported since 2019 as a result of a worker being crushed by a bucket that fell from a quick coupler. While quick couplers have their own individual safety specifications, it is important to note that employers must ensure their workers are never working beneath a bucket, attachment, or load, and that workers should never be within the swing radius of an operating excavator. If workers are located outside of this hazard zone, there is much less risk of injury or death if a failure occurs. Furthermore, OSHA prohibits working beneath a load or within the swing radius of an excavator [3-6], and manufacturer and industry guidelines provide strong language recommending against this all-too-common practice [7-11]. If these guidelines are not followed, injuries and death can occur.
Case Studies/FACE Reports
As part of its ongoing mission, the NIOSH Fatality Assessment and Control Evaluation (FACE) program aims to prevent occupational fatalities across the nation by identifying and investigating work situations at high risk for injury, and then formulating and disseminating prevention strategies to those who can intervene in the workplace.
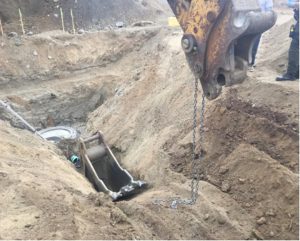
California is one of the states funded by NIOSH to perform fatality assessments and recent excavator quick coupler deaths in that state have led the California FACE program to share findings from their investigations to improve worker safety:
- California FACE Case Study #1: A 67-year-old pipefitter was killed while working in a trench below the bucket of an excavator using a quick coupler device (Figure 3). The quick coupler likely suffered a mechanical failure, and the bucket detached while digging, landing on the 15-year-veteran pipefitter and killing him. There was no one on site designated as an OSHA competent trench supervisor to prevent the worker from standing beneath the bucket [13].
- California FACE Case Study #2: A 21-year-old heavy equipment trainee was killed when he attached a bucket using a quick coupler and stood below the bucket to inspect it. There were no records of the young worker receiving excavator safety training, and he elevated the boom in order to inspect the bucket from below. The bucket detached while the worker was below the bucket and was immediately killed from his injuries [14].
These case studies, combined with other research, demonstrate that most quick coupler failures are a result of a combination of the following: inadequate training or supervision, engineering or mechanical failures, operator error, or work culture that dismisses the hazard [15,16,17].
Prevention
Workers should be trained to always assume that a quick coupler has the potential to fail and should never be below a bucket, attachment, or other load.
Employers need to provide training and on-site competent supervision to ensure no employees enter an area that puts them in danger. Likewise, workers and operators must adhere to training guidelines and safe practices to protect themselves. The common theme in the two California FACE case studies is that a worker was standing below an elevated load. As noted earlier, OSHA prohibits working below an elevated load, and manufacturers and industry associations state that workers should never be beneath an elevated load. If a load falls unexpectedly, either from improper attachment of a quick coupler device or a mechanical failure, death or serious injury can occur.
Following are recommendations to prevent injuries or fatalities from excavators with quick coupler devices:
- First and foremost, maintain work practices and administrative procedures to keep workers away from an elevated load and out of the swing radius of both the excavator dipper arm and the excavator superstructure.
- Ensure a training program has been implemented for operators who use quick couplers.
- Always ensure the quick coupler is properly engaged by using approved safety checks, visual indicators, and/or warning devices. If required by the manufacturer, the safety locking pin must be in place prior to lifting the attachment off the ground [18].
- Prior to using an attachment, always perform a connection test as specified by the manufacturer [7, 8,15,18].
- Adhere to regular maintenance of the quick coupler device according to manufacturer guidelines [15,18].
- If a quick coupler or an attachment needs to be inspected, do not approach the device unless the attachment is lowered and resting on the ground. This is equally important for manually attached quick couplers that require a worker to secure the attachment or manually place a manufacturer-specified safety locking pin [18].
- Use only manufacturer-approved and compatible attachments.
- Install retrofit safety kits on older quick coupler devices or upgrade to newer quick couplers with built-in safety mechanisms. Human detection systems may also be available in some newer excavators to prevent contact with a worker who is within the swing radius [15,17,19,20].
Lessons learned from fatalities involving excavator quick couplers show that these time-saving devices can be dangerous. Employers need to train operators to use caution when other workers are nearby, maintain and inspect equipment properly, and ensure the attachments are correctly secured prior to use.
National Stand-Down to Prevent Struck-By Incidents
The National Occupational Research Agenda (NORA) Construction Sector Council is undertaking a number of initiatives to increase awareness of struck-by hazards and ways to prevent them, including coordinating the annual National Stand-Down to Prevent Struck-by Incidents.
The 3rd annual National Stand-Down to Prevent Struck-by Incidents is taking place April 11 – 15, 2022. This year there will be free webinars on work zone safety, lift zone/heavy equipment safety, and dropped objects to raise awareness on these hazards and what companies can do to prevent these struck-by incidents. Companies are encouraged to conduct a Safety Stand-Down by taking a break to have a toolbox talk, conducting safety equipment inspections, or discussing job specific hazards. Managers are encouraged to plan a stand-down anytime that works best for their workplace.
Laura Styles, MPH; Hank Cierpich; Robert Harrison, MD, MPH – California Department of Public Health
David Schutt, MS, PhD Student Colorado State University
Scott Earnest, PhD, PE; CSP; Nancy T. Romano M.S., CSHM; CDR Elizabeth Garza, MPH, CPH; J’ette Novakovich, PhD, MS, MA; Douglas Trout, MD, MHS; and LT Bryan Wimer – National Institute for Occupational Safety and Health
References
[1] Wang, X. W., Katz, R., Schneider, S., Memarian, B., & Dong, X. W. (2018). Struck-by injuries and prevention in the construction industry. The Center for Construction Research and Training, Silver Spring. https://www.cpwr.com/wp-content/uploads/publications/Quarter2-QDR-2017.pdf
[2] Dong, Xiuwen & Wang, Xuanwen & Katz, Rebecca. (2018). The sixth edition of The Construction Chart Book – The U.S. Construction Industry and Its Workers, Chart 43d. https://www.cpwr.com/research/data-center/the-construction-chart-book/chart-book-6th-edition-fatal-and-nonfatal-injuries-leading-causes-of-fatal-and-nonfatal-injuries-in-construction/
[3] Occupational Safety and Health Administration. (1994). Occupational safety and health standards: Occupational health and environmental control: Occupational noise exposure (OSHA Standard No. 1926.651). United States Department of Labor. https://www.osha.gov/laws-regs/regulations/standardnumber/1926/1926.651
[4] Occupational Safety and Health Administration. (2015). Occupational safety and health standards: Occupational health and environmental control: Occupational noise exposure (OSHA Standard No. 1926.21). United States Department of Labor. https://www.osha.gov/laws-regs/regulations/standardnumber/1926/1926.21
[5] Occupational Safety and Health Administration. (2003). United States Department of Labor. https://www.osha.gov/laws-regs/standardinterpretations/2003-01-16-0 (Accessed Feb. 7, 2022).
[6] Occupational Safety and Health Administration. (1970). Occupational safety and health standards: Occupational health and environmental control: Occupational noise exposure (OSH Act of 1970 Section 5(a)(1)). United States Department of Labor. https://www.osha.gov/laws-regs/oshact/section5-duties
[7] Hill Tefra Installation and User Manual. (2015). Newry, County Down, Northern Ireland. https://www.hillattach.com/wp-content/uploads/2020/08/tefra_coupler_user_manual.pdf (Accessed Feb. 7, 2022).
[8] Werk-Brau Co., Inc. D-Lock Coupler Installation and Operation Manual. https://werk-brau.com/wp-content/uploads/2019/12/D-Lock-Manual-Rev-F.pdf (Accessed Feb. 7, 2022).
[9] Komatsu Construction. (Oct. 29, 2018). Komatsu Safety – Avoiding Pinch Points [Video]. YouTube. https://youtu.be/V8s_YAc3svA?t=131 (Accessed Feb. 7, 2022).
[10] Cat® Products. (Aug. 16, 2021). Safety Tips for your Cat® Excavator [Video]. YouTube. https://youtu.be/CJM_qHYXJDA?t=77 (Accessed Feb 7, 2022).
[11] Doosan Infracore North America. (Dec. 11, 2015). Doosan Excavators: Heavy Equipment Training & Safety [Video]. YouTube. https://youtu.be/CDXS2ZFjvrc?t=706 (Accessed Feb. 7, 2022).
[12] Association of Equipment Manufacturers (AEM). (2010). AEM Safety Manual for Hydraulic Excavators. Milwaukee, WI. https://shop.aem.org/AEM%20Safety/aem-safety-products/hydraulic-excavator-safety-manual/ (Accessed 1/27/2022).
[13] CA/FACE (Aug. 4, 2021). https://www.cdc.gov/niosh/face/pdfs/20ca002.pdf
[14] CA/FACE (July 2, 2021). https://www.cdc.gov/niosh/face/pdfs/20ca001.pdf
[15] Occupational Safety and Health Administration (OSHA). (July 22, 2005). Hazards of Inadequately Securing Hydraulic Excavator Buckets When Using Quick Coupling Devices. Safety and Health Information Bulletin. https://www.osha.gov/sites/default/files/publications/shib072205a.pdf
[16] Edwards, D. J., & Holt, G. D. (2008). Health and safety issues relating to construction excavators and their attachments. Engineering, Construction and Architectural Management. https://www.researchgate.net/profile/David-Edwards-59/publication/235318803_Health_and_safety_issues_relating_to_construction_excavators_and_their_attachments/links/58fb24a30f7e9ba3ba5201dc/Health-and-safety-issues-relating-to-construction-excavators-and-their-attachments.pdf
[17] Rinneberg, S., Teizer, J., Kessler, S., & Günthner, W. A. (2015). Smart quick coupling system for safe equipment attachment selection and operation. In ISARC. Proceedings of the International Symposium on Automation and Robotics inConstruction (Vol. 32, p. 1). IAARC Publications. http://www.iaarc.org/publications/fulltext/FFACE-ISARC15-2997841.pdf
[18] National Institute for Occupational Safety and Health (NIOSH). (Nov. 2003). Preventing Injuries When Working With Hydraulic Excavators and Backhoe Loaders. Workplace Solutions Publication No. 2004-107. https://www.cdc.gov/niosh/docs/wp-solutions/2004-107/pdfs/2004-107.pdf
[19] Jo, B. W., Lee, Y. S., Kim, J. H., Kim, D. K., & Choi, P. H. (2017). Proximity warning and excavator control system for prevention of collision accidents. Sustainability, 9(8), 1488. https://www.mdpi.com/2071-1050/9/8/1488/htm
[20] Son, H., Seong, H., Choi, H., & Kim, C. (2019). Real-time vision-based warning system for prevention of collisions between workers and heavy equipment. Journal of Computing in Civil Engineering, 33(5), 04019029. https://ascelibrary.org/doi/abs/10.1061/%28ASCE%29CP.1943-5487.0000845
Posted on by