National Marble Day: A Look at the Manufacturing of Glass Marbles
Posted on by
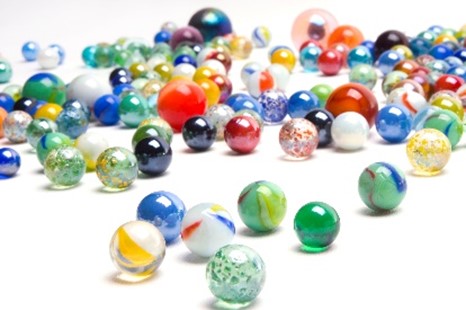
The blog content comes from the NIOSH Manufacturing Mondays series.
July 23rd is National Marble Day. There is much more to these little spheres than you might think. Although the game of marbles was originally played by children, it grew into a fun pastime for adults as well. There are treasure hunts to find special marbles; collectors seek out old marbles as well as the beautiful creations of modern glass makers.
Marbles have been used for play for thousands of years. In ancient Rome, nuts were used as game pieces. These were eventually replaced by clay balls. However, clay was easily worn or chipped. Marbles made from marble or other stones were produced by powered mills in 17th century Germany [Incidentally, the word marble is derived from the German word “for the rock”]. Glass marbles ultimately came into being around the middle of the 1800’s. It is believed that they were first created by glassmakers who shaped bits of leftover glass at the end of the day to take home for their children. However, it was not long before the process was automated with factories turning out large quantities.
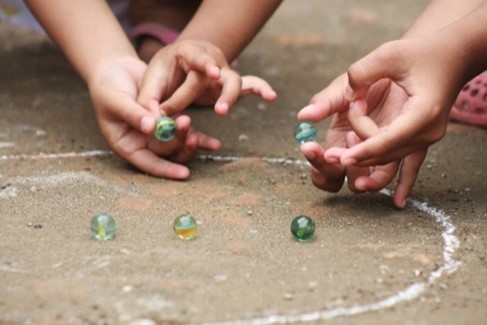
Marbles are not only for games. The mixing ball in a can of spray paint is a marble. They are also used in air and water filtration systems. They make up the reflective letters on road signs and have been used in NASA weather balloons.
Most glass marbles are made commercially today in an automated process. The raw materials used for marbles include sand, soda lime, silica, and other materials for color. Scrap glass, cullet, is often included or even the primary ingredient. The materials are combined in a furnace and heated at 2300 °F for 24 hours or longer. The liquid glass moves to a flow tank from which small globs of glass are released and then cut to size. These small globs roll down ramps and into grooved rollers that create spheres from the globs and cool the molten glass. After completely cooling, the marbles are sorted and packaged.
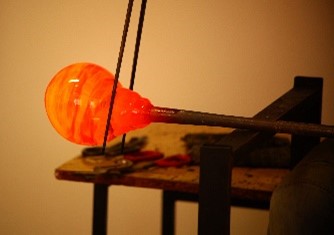
Larger, collector marbles are hand-crafted in a glassworks studio. These require the artistry of a glass blower and can involve intricate designs. These are more likely to be found in a display case than in a game of marbles!
Modern marble manufacturers experience several health and safety concerns. The raw materials may cause exposure to hazardous particulates as they are loaded into the melting furnace. Fumes may also be released from the heated materials. To address these concerns, proper ventilation is critical in this area. Respiratory protection may also be needed along with an appropriate respiratory protection plan. The furnaces that melt the glass components and the tanks that hold molten glass are at dangerously high temperatures. Heat stress and burns are potential hazards in these areas that must be addressed. The automated rolling machines have pinch hazards along with the potential for burns. Machinery should be properly guarded, and employers should train their workers on how to avoid hazards. To address eye hazards from breaking glass, as well as the radiation that comes from using a torch when creating art pieces, appropriate eye protection should be used. Noise from the furnaces and cutting/rolling machinery is another potential hazard; hearing protection should be utilized where appropriate.
Instead of playing on your phone, maybe bring out some marble games and get mesmerized in the refracting light, excited by the cracking collisions, or simply relaxed by rolling them around.
For more information:
Mountain Glass Arts | Health and Safety Guidelines
How Products are Made | Marbles
NAICS Code 327991 – Cut stone and stone product
Jenny Topmiller, MS, NIOSH Manufacturing Sector Program Co-Coordinator.
RJ Matetic, MS, PhD, NIOSH Associate Director for Manufacturing.
Gary Roth, MS, PhD, NIOSH Manufacturing Sector Program Co-Coordinator.
Richard Current, PE, NIOSH Manufacturing Sector Program Assistant Coordinator.
Adam Smith, PhD, NIOSH Manufacturing Sector Program Assistant Coordinator.
The Manufacturing Program highlights activities within the program and throughout the world of Manufacturing. To share your ideas for future topics contact us at mnf-program@cdc.gov.
Posted on by