The Use of Real-time Respirable Dust Monitors
Posted on bySensors are an increasing presence in our lives—from wearable gadgets to smart buildings, from autonomous vehicles to smart cities. In occupational health and safety, sensors are used widely for exposure monitoring, emergency response, and safer worker-machine interfaces. The use of sensors as real-time respirable dust monitors is a targeted application with its own specific challenges. The information from real-time respirable dust monitors can be used to identify tasks and activities throughout the workday, during which the worker might be exposed to higher than average concentration levels. The monitors can assess the efficacy and efficiency of engineering control technologies and work practices. In the future, dust sensors might be employed for smart adjustments of control technologies. The first real-time dust monitors used in occupational environments were bulky, complicated to use, and with limited functionalities. Since then, these monitors have become small enough for personal monitoring, with advanced displays and software, and in some cases are capable of transferring and sharing data in real time via Bluetooth and cloud technology. As their popularity increases, it is important to understand how well these monitors perform.
Components of a Personal Dust Monitor
While each commercially available real-time respirable dust monitor might have specialized features, there are three common components: a size selector, a sensing element, and an optional filter media. When using a respirable dust monitor, the operator is sure to focus on respirable dust by the presence of a proper size selector, a cyclone, or an impactor stage. The flowrate at which the respirable dust monitor is used is critical and specific for each size selector type.
The sensing element in a real-time respirable dust monitor is the core of the measurement. Most monitors currently on the U.S. market function as optical particle counters: The dust particles interact with a light beam generated by a source, the interaction generates scattered light that is received by the detector and transformed by an algorithm into corrected data such as mass concentration. The mass concentration reading is not the direct measurement of the mass of dust—it is the product of a mathematical algorithm from an indirect measurement.
Finally, some real-time respirable dust monitors collect the dust on a filter for post-analysis. The analysis of the sample collected is useful to verify and correct the results of the mathematical algorithm and it can be used for offline investigations—i.e., for crystalline silica, or perhaps for identifying elemental composition such as metals.
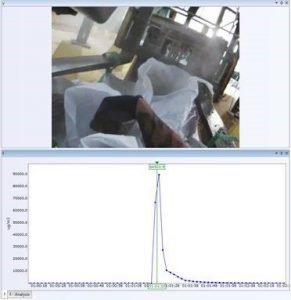
Helmet-CAM provides missing exposure information
The NIOSH Mining Program has extensive experience in the development of real-time dust monitors and monitoring approaches. Recently a new monitoring approach called Helmet-CAM was designed. This approach tackles the only information that is still missing when adopting real-time personal respirable dust monitors: real-time information about the specific tasks performed by the worker during the day. The solution is a small camera attached to the helmet of the worker or on the shoulder, which records the worker’s activities in real time so they can shortly thereafter be synced with the worker’s exposure levels. Combining the information from the monitor and the Helmet-CAM is now possible by using the NIOSH software, EVADE, available to the public free of charge. Combining Helmet-CAM hardware components and EVADE software, has had a tangible impact on both workers’ exposure to respirable dust as well as their perception of the health hazard.
A Revealing Real-time Monitoring Study
The large amount of data generated by the extensive use of personal real-time dust monitors is also of interest. Recently, a study was initiated to investigate aggregated information gathered over 10 stand-alone monitoring sessions involving over 80 miners. The purpose of the study was to assess if an algorithm could be designed to objectively analyze the data very quickly and to determine if the elevated exposures were the result of distinct events—as these events are most often related to the most serious dust emissions, and engineering controls or work practice improvements should be quickly focused here. The algorithm identified respirable dust concentration levels that were more than 10 times the mean (threshold value) for the measurement session. Those values greater than the threshold were then removed and the new resulting mean calculated as well as the mean dust reduction.
The preliminary findings from the analysis of over 144 hours of combined sampling aggregation were the following:
- Episodes during the workday when the respirable dust mass concentration was substantially higher than the average (10 times) were generally limited in time—on average close to 2 minutes (112 seconds).
- For the specific aggregate data considered for this study, the high dust mass concentration episodes occurred 2% of the overall monitoring time—translated to an 8-hour work shift, this means only ten minutes.
- While the accuracy of the real-time dust monitor to measure the respirable dust mass concentration associated with these episodes is limited and to be determined—the next section explains the issue—the impact on the mean concentration is substantial because the mean concentration drops 20% or more simply by addressing these spikes.
- Combining the results, the data shows how important it is to address short, “limited in time” episodes of elevated respirable dust mass concentration levels to lower the average exposure of workers.
Testing Real-time Dust Monitor Performance
The accuracy of the data generated by real-time respirable dust monitors is a topic of great interest, and it influences how the monitors are used. Another recent study evaluated the performance of three commercially available real-time respirable dust monitors—used in the Helmet-CAM approach—in a controlled dust chamber. Each monitor was freshly calibrated by the manufacturer. The performance of the real-time dust monitors was tested using traditional samplers side-by-side with a common standard aerosol—Arizona Road Dust (A1-fine). For each monitor, a correction factor was calculated, with a procedure that any user should employ with a new dust. While the manufacturers of these particulate monitors recommend such calibration for each new dust, it is unclear how common this procedure is in practice. Preliminary results showed that the correction factor values on average ranged from 0.85 to 1.5. Arizona dust is commonly considered a standard material amongst aerosol scientists as well as real-time respirable dust monitor manufactures, therefore it was both surprising and concerning that the correction factor was not one for any instrument. The NIOSH Mining program is planning to publish the full set of results in the coming months.
Next Steps
More research is needed to fully investigate the performance of commercially available real-time respirable dust monitors—i.e., the factory calibration, the inter-unit precision, whether the response based on the type of respirable dust and environmental conditions can be modeled, and what industrial hygienists need to know and can do to use these monitors to the best of their performance capabilities. To accomplish these tasks, direct interaction with companies that develop and commercialize the monitors can be helpful. In addition, the use of the large amount of data generated by these monitors and their role in a mine’s health and safety management system are topics of interest for NIOSH researchers and other professionals.
With these ideas in mind, the NIOSH Center for Direct Reading and Sensor Technologies has recently launched a new initiative—“right sensors used right”—that will focus on the correct selection and use of real-time monitors. The first focus for the initiative will indeed be real-time respirable dust monitors. Activities will be organized in the coming months, and we look forward to discussion on this topic with industry stakeholders on this blog below and in other forums.
Emanuele Cauda, PhD, is a Senior Service Fellow in the NIOSH Pittsburgh Mining Research Division. He is also the Deputy Director of the NIOSH Center for Direct Reading and Sensor Technologies.
Justin Patts, BSME, is a mechanical engineer in the NIOSH Pittsburgh Mining Research Division.
Posted on by